Surface roughness: | Ra≤25μm; | Payment Terms: | L/C,T/T; |
Table Travel (Y) (mm): | 2000; | Port: | ShangHai Port; |
run soeed: | 20m/min; | Cutting positioning accuracy: | ±5mm/m; |
Effective Cutting area(width): | 3000mm; | Model Number: | ACWJ-1530; |
Cutting Accuracy(mm): | 0.01; | Effective Cutting area(Length): | 1500mm; |
Applicable Industries: | Hotels,Building Material Shops,Machinery Repair Shops,Manufacturing Plant,Construction works ; | After Warranty Service: | Video technical support,Online support; |
Brand Name: | ACCURL; | Certification: | CE ISO; |
Key Selling Points: | High-accuracy; | Weight (KG): | 6500; |
Place of Origin: | Jiangsu China; | Packaging Detail: | Steel Pallet for Water jet Cutting Machine; |
Warranty: | 3 years; | Repeatability (X/Y/Z) (mm): | ±0.001; |
Dimension(L*W*H): | 3880*2150*2000mm; | Year: | 2021; |
Local Service Location: | Japan,Malaysia,Australia,Morocco,Chile,Colombia,Romania,South Africa,Canada,United Kingdom,United States,Italy,France,Germany,Viet Nam,Philippines,Peru,Saudi Arabia,Indonesia,India,Mexico,Russia; | Video outgoing-inspection: | Provided; |
Number of Axes: | 5; | Rated Power: | 7.5 KW; |
Condition: | New; | Type: | Water Jet Cutters; |
Core Components: | PLC,Engine,Bearing,Gearbox,Motor; | Table Travel (X) (mm): | 1500; |
Marketing Type: | Hot Product 2019; | Warranty of core components: | 2 years; |
Table Travel (Z) (mm): | 3000; | Application: | Industrial Metal Cutting; |
Weight: | 6500Kgs; | Supply Ability: | 10 Set/Sets per Day; |
After-sales Service Provided: | Engineers available to service machinery overseas,Online support,Video technical support; | Package Preview: | ; |
Showroom Location: | Morocco,Chile,Colombia,Romania,South Africa,Japan,Malaysia,Australia,Canada,United Kingdom,United States,Italy,France,Germany,Viet Nam,Philippines,Peru,Saudi Arabia,Indonesia,India,Mexico,Russia; | Voltage: | 380V 220V Optional; |
Machinery Test Report: | Provided; | | |
Products Description
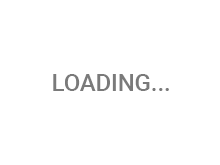
3015 SERIES WATERJET CUTTING MACHINE 50HP
The ACCURL MAX-WJ CNC waterjet cutting series is an addition to Accurl MAX-WJ CNC waterjet cutting machine line. It provides a vigorous industrial design and rigid construction that combines precision and simplicity. The
MAX-WJ model is made to handle high production for versatile applications. The MAX-WJ waterjet cutting series provides a vigorous industrial design and rigid construction that combines precision and simplicity. The MAX-WJ model is made to handle high production for versatile applications. The MAX-WJ models come in two distinct sizes for the most common applications.
TECHNOLOGICAL ADVANTAGES * The most versatile cutting systems on the market today, covering the full range of materials and thicknesses, even painted surfaces.
* Low cutting temperatures to prevent thermal alteration and residual tension.
* Clean cut without harmful atmospheres
* The cut surface neither cracks nor bends.
* Optimal utilization of raw material with negligible material loss
* Eliminates subsequent finishing processes.
* Ability to perform different types of cutting simultaneously
* Very strict tolerances..
FULLY ANNEALED FRAME
* ACCURL®steel frames undergo annealingat over 600⁰ to relieve stress.they are built to last years of heavy use withoutdistortion.
* Very stiff and stable base frame
* Dual synchronized twin servo motor drive system.
* Stress points analysis
* Usage of high-tech boring machines for extreme precision parts.
CAST ALUMINIUM GANTRY
ACCURL®s high tech Mn-steel crossbeam allows better rigidity at 50% of the weight of traditional iron gantries, allowing higher acceleration with reduced inertia.this creates less wear and tear on the machine.
YASKAWA SERVO MOTORS & DRIVES
* The Smartline is equipped with cutting edge Germany designed
* YASKAWA servo motors and drives from Japan.
* High-speed EtherCAT communication
* Highly dynamic behaviour
* Brushless three-phase motors
* Flexible motor type selection
TRANSMISSION SYSTEM
* ACCURL® Waterjet are provided are equipped with constituted by a solid structure in order to assure the best repetitiveness and high precision in axes positioning.
* X ,Y-Axis with HIWIN linear guide and Ball Screw.
* Less noise, greater durability and greater precision.
* Unprecedented positioning repeatability of ±0.05 (optional ±0.01).
HIGH PRESSURE PUMP
The high pressure is generated in the intensifier of the pump, actuated by an oil pump inside, and also the low water supply system. The latest generation of pumps offers the most advanced water jet technology with working pressures Up to 4200 bar. The design with a single intensifier, which generates up to 4200 bar, reduces maintenance costs and offers a quieter operation and fewer spare parts.
Technical specifications | | The high-pressure pump is characterized by: |
Nominal power | 37 kW / 50 HP | •Hydraulic pump of variable flow and compensated pressure |
Maximum working pressure | 4136 bar | •High / low pressure selection that allows piercing |
Maximum flow | 4.1 L/min | •Electrical inversion of the cutting head |
Hydraulic tank capacity | 211 L | •Noise level below 80dB |
Pressure accumulator volume | 1 L | •Leakage detection in de high-pressure circuit |
Water inlet pressure | 2.4 - 5.5 bar | •Long lasting high pressure seals |
Nominal current | 72 A | •System to uninstall de piston without uninstalling the cylinder |
Protection at 400 V / 50 Hz | 80 A | •Air / oil heat exchanger |
Noise level | 76 dB | •Cost-effective Cutting System |
Length x Width Height | 1689x1114x1508mm | •Maintenance-free Operation |
Weight | 1438 Kg | •The sensors, located before and after the booster pump |
AUTO SULLAGE REMOVAL SYSTEM 2.0
Electronic height adjustment system for the cutting head, which guarantees the constant distance between the nozzle and the cutting material, offering the possibility of cutting materials with uneven surfaces..
AUTO SULLAGE REMOVAL SYSTEM 2.0
This unit will condition the incoming water to the intensifier, removing lime from the water. It is highly recommended to install it to ensure filtration and decalcification of the water used for cutting, prolonging the life of all the high-pressure
components.
AUTONOMOUS ABRASIVE FEEDER-ABRALINE 3.0 | |
Net weight | 80 kg |
Length | 700 mm |
Width | 700 mm |
Height | 1400 mm |
Storage deposit capacity | 200 l |
Pressurized tank capacity | 24 l |
Minimum working pressure | 5 bar |
Maximum working pressure | 7 bar |
Maximum compressed air consumption | 500 l/min |
Maximum abrasive flow rate | 1.300 gr/min |
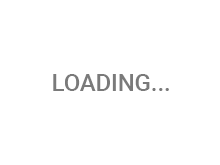
NEW ECS905 CNC WITH COMMAND CONTROL
* The ACCURL Masterline Fiber Laser is controlled with a ECS900 CNC control unit which provides unprecedented control of the cutting process.
* Real time graphics: the program is provided with a manual and/ or an automatic zoom to visualize the plate contour.
* Automatic restore after work stoppage. After repositioning on the profile, there is the option to return to tangential or
linear mode, with activation of cutting on or external to the profile.
* EtherCAT and eXtreme Fast Control (XFC) technology enable fast switching functions at high processing speeds.
* The CNC 900 series can control up to 16 interpolated axes (axis or spindle) and the TwinCAT NC I/CNC automation software is ideally suited for application-specific functions, including adaptive jet control, reverse travel or path resetting.
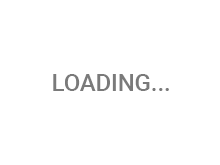
CAD/CAM SOFTWARE NESTING. LIBELLULA .CUT
* Libellula.CUT is the cutting edge of Libellula Universe andrepresents the highest expression of the technological know-how of Libellula.
* Thanks to its integrated CAD and the exclusive One-Clicktechnology, Libellula.CUT creates or imports in a moment the geometric details from any other platform of drawing, automatically optimizing profi les and arranging them in an optimum manner for subsequent processing.
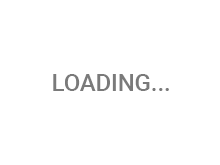
THE MAX 3D 5-AXIS CUTTING HEAD 2.0
The 3D cutter head has five axes, 3 linear and 2 rotating. It has been designed for both pure 3D cut and 2D 1/2 cut (flat cut with bevel), without losing 2D (flat) cut functionality. Its design features offer great work possibilities. Especially its infinite rotation in the C axis, which avoids the need to rewind with a consequent reduction in working times and a lower risk of reducing the cut quality. On the rotating frame of the C-axis, it is possible to connect the height adjustment and anti-collision control module.
Sample Presentation
Related Products
Hydraulic Guillotine Shearing Machine
CNC TURRET PUNCHING MACHINE
Company Profile
WHY CHOOSE ACCURL ?
ACCURL is a famous manufacturer of metal sheet equipments in world market. Its Brand ¡°Accurl¡± has been leading brand for many years in the field of international metal sheet equipments. Our group devote ourselves to product development, production and sales.
Our main products are: CNC Press Brake, Shears, Hydraulic press, Laser Cutter and CNC rolling machine these sheet metal processing equipments.we are using advanced technology from German, Japan, and Italy.we can produce large Hydraulic Press and Press Brake more than 16000 ton & 16m.we are with professional R&D team, and we have World-class design and manufacturing capabilities.
Exhibition
Product packaging
We are currently reviewing our product packaging from the angles of waste-reduction and resource-saving. We are also working on improving transportation efficiency from the design phase of product development.1.Our wooden case is after fumigation treatment. Needn't timber inspection, saving shipping time.
2.All the spare parts of the machine were covered by the some soft materials mainly using pearl wool.
3.The outmost is wooden case with fixed formwork.
4.The bottom of the wooden case has firm iron jack, convenient to handing and transport.
Our Serives
The use of an interferometer records the machines X and Y axis movement during cutting to ensure accuracy.
Adjustments are made to ensure machine is precisely tuned before shipment.
A Marble test is performed to measure the X and Y axis, calculating any necessary adjustments to ensure perfect level and alignment along length of machine.
A collimator is run along the full length of the guide rail, testing for
straightness. Adjustments are made as required to ensure linear accurae linear accuracy.
FAQ
1.Can you supply the relevant documentation?Yes, we can provide most documentation including Certificates of Analysis / Conformance; Insurance; Origin, and other export documents where required.
2.What is the average lead time?
For samples, the lead time is about 7 days. For mass production, the lead time is 20-30 days after receiving the deposit payment.
The lead times become effective when (1) we have received your deposit, and (2) we have your final approval for your products. If our lead times do not work with your deadline, please go over your requirements with your sale. In all cases we will try to accommodate your needs. In most cases we are able to do so.
3.What kinds of payment methods do you accept?
You can make the payment to our bank account, Western Union or PayPal:30% deposit in advance, 70% balance against the copy of B/L.
4.What is the product warranty?
We warranty our materials and workmanship. Our commitment is to your satisfaction with our products. In warranty or not, it is the culture of our company to address and resolve all customer issues to everyone’s satisfaction.
5.Do you guarantee safe and secure delivery of products?
Yes, we always use high quality export packaging. We also use specialized hazard packing for dangerous goods and validated cold storage shippers for temperature sensitive items. Specialist packaging and non-standard packing requirements may incur an additional charge.
6.How about the shipping fees?
The shipping cost depends on the way you choose to get the goods. Express is normally the most quickest but also most expensive way. By seafreight is the best solution for big amounts. Exactly freight rates we can only give you if we know the details of amount, weight and way. Please contact us for further information.