Product name: | Cement Production Plant Line; | Capacity: | 100-6000tpd; |
Brand Name: | TongLi; | Core Components: | Engine,Gearbox,Motor,Pressure vessel,Gear,Pump; |
Supply Ability: | 100 Sets per Year; | Port: | Shanghai/Ningbo Port; |
After Warranty Service: | Video technical support,Online support,Spare parts,Field maintenance and repair service; | Warranty of core components: | 1 Year; |
Dimension(L*W*H): | Depending on capacity; | Video outgoing-inspection: | Provided; |
Package Preview: | ; | Keyword: | Cement Plant Cement Production Line; |
Place of Origin: | Zhejiang, China; | Condition: | New; |
Marketing Type: | New Product 2020; | Key Selling Points: | Energy saving; |
Local Service Location: | Egypt,Canada,Philippines,Pakistan,India,Russia; | Weight: | 850000 kg; |
Payment Terms: | L/C,Western Union,T/T,Paypal; | Packaging Detail: | 1.Standard container 2. Nude packing 3. Wooden box; |
Showroom Location: | None; | Application: | Cement Clinker; |
Voltage: | 220/380/440v; | After-sales Service Provided: | Engineers available to service machinery overseas,Online support,Free spare parts,Field installation, commissioning and training,Field maintenance and repair service,Video technical support; |
Applicable Industries: | Construction works ,Energy & Mining; | Certification: | CE,TUV,ISO,BV; |
Warranty: | 1 Year; | Color: | Customizable; |
Power: | 800-20000KW; | Machinery Test Report: | Provided; |
Product Description
The cement production line (cement plant) is a cement equipment production line composed by a series of equipment. This production line mainly consists of the process of crushing and prehomogenization, raw materials homogenizing, preheating decomposition, cement clinker firing, cement grinding & packaging.
The main equipments used in this whole production line include the vibrating feeder, jaw crusher, impact crusher,Raw material vertical mill, cement ball mill lifer, preheating system, cement rotary kiln and packing machine and so on. All the cement equipment in this line can be provided by our factory.
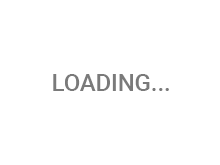
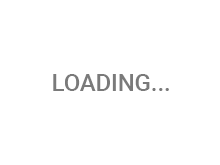
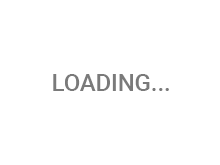
1.Crushing and pre homogenization
(1) Crushing: in the process of cement production, most raw materials need to be crushed, such as limestone, clay, iron ore and coal. Limestone is a raw material with large amount of cement production. After mining, the particle size is large and the hardness is high. Therefore, limestone is a raw material with large amount of cement production. After mining, the particle size is large and the hardness is high. The crushing process is more economical and convenient than the grinding process. Break large materials to small and uniform particle size as much as possible, so as to reduce the load of grinding equipment and improve the output of grinding machine. After the materials are broken, the separation of materials with different particle sizes in the process of transportation and storage can be reduced, the raw meal with uniform composition can be prepared, and the accuracy of batching can be improved.
(2) Raw material pre homogenization: raw material pre homogenization is that when materials are stacked, the incoming raw materials are continuously stacked by the stacker into as many material layers parallel to each other, overlapping up and down and of the same thickness as possible. When taking materials, cut all material layers at the same time as far as possible in the direction perpendicular to the material layer, and cut them in turn until they are taken, i.e. "tile and straight take". Make the raw material storage yard have the functions of storage and homogenization at the same time.
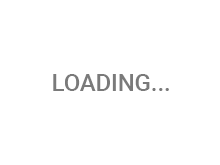
2. Raw meal preparation
(1) Raw material proportioning: there are four proportioning silos (or other special auxiliary material silos) for raw material proportioning: limestone, sandstone, iron ore and fly ash. Weighing feeders are set at the bottom of the silo to give various materials quantitatively according to the proportion required by the production process. It is sent to the vertical grinding system by belt conveyor for grinding.
(2) Raw material grinding: the materials fall to the center of the grinding plate through the blanking chute through the air lock feeding device, are thrown to the edge of the grinding plate under the action of centrifugal force, and are rolled and ground by the grinding roller. The crushed materials overflow from the edge of the grinding plate and are dried by the hot air flow from the nozzle at a high speed upward. According to the different air flow speed, some materials are brought into the high-efficiency powder concentrator by the air flow, After separation, the coarse powder is returned to the grinding plate for re grinding; The qualified fine powder flows out of the mill with the gas and is mixed with the dust collected by the humidification tower and electrostatic precipitator, and sent to the raw material homogenization warehouse for homogenization and storage through chute and bucket elevator
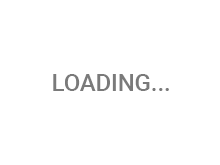
3. Raw meal homogenization
When the raw meal powder is unloaded downward, it is stirred by air and acted by gravity to produce "funnel effect". Try to cut multi-layer material surface and mix fully. Different fluidizing air is used to make the parallel material surface in the warehouse have fluidizing expansion of different sizes. Some areas are unloaded and some areas are fluidized, so that the material surface in the warehouse is inclined for radial mixing and homogenization. In the process of cement production, stabilizing the composition of raw materials entering the pit is the premise of stabilizing the thermal system of clinker burning, and the raw material homogenization system plays the latter role of stabilizing the composition of raw materials entering the pit.
4. Preheating and pre decomposition
The preheating and partial decomposition of the raw material are completed by the preheater instead of some functions of the rotary kiln, so as to shorten the length of returning to the kiln, and make the gas material heat exchange process in the accumulated state in the kiln move to the suspended state in the preheater, so that the raw material can be fully mixed with the hot gas discharged from the kiln, increase the gas material contact area, fast heat transfer speed and high heat exchange efficiency, The purpose of improving the production efficiency of the kiln system and reducing the heat consumption of clinker burning is achieved.
(1) Preheater: the main function is to make full use of the waste heat of the waste gas discharged from the rotary kiln and calciner to heat the raw meal, so as to preheat the raw meal and decompose some carbonate. In order to greatly improve the heat exchange efficiency between gas and solid and realize the high quality, high yield and low consumption of the whole calcination system, it is necessary to have three functions: uniform gas-solid dispersion, rapid heat exchange and efficient separation.
(2) Pre decomposition: the emergence of pre decomposition technology is a technological leap in cement calcination process. It is to add a decomposition furnace between the preheater and the rotary kiln, use the rising flue at the kiln tail, and set up a fuel injection device, so that the exothermic process of fuel combustion and the endothermic process of carbonate decomposition of raw meal can be carried out rapidly in the decomposition furnace in suspended or fluidized state, so as to increase the decomposition rate of raw meal into the kiln to more than 90%. Move the original carbonate decomposition task in the rotary kiln to the decomposition furnace; Most of the fuel is added from the calciner and a few from the kiln head, which reduces the heat load of the calcination zone in the kiln, prolongs the service life of the lining and is conducive to large-scale production; Due to the uniform mixing of fuel and raw meal, the combustion heat of fuel is transferred to materials in time, so that the combustion, heat exchange and carbonate decomposition process are optimized. Therefore, it has a series of excellent properties and characteristics such as high quality, high efficiency and low consumption.
5. Firing of cement clinker
After the raw meal is preheated and pre decomposed in the cyclone preheater, it enters the rotary kiln for clinker burning. In the rotary kiln, carbonate further decomposes rapidly and a series of solid-state reactions occur to produce AC3, afc4, SC2 and other minerals in cement clinker. With the increase of material temperature near c01300, minerals such as AC3, afc4 and SC2 will become liquid phase, and SC2 dissolved in liquid phase will react with Cao to produce a large amount of SC3 (clinker). After the clinker is fired, the temperature begins to decrease. After that, the high-temperature clinker discharged from the rotary kiln is cooled by the cement clinker cooler to the set temperature of the storage warehouse for storage. At the same time, the sensible heat of the high-temperature clinker is recovered to improve the thermal efficiency and clinker quality of the system.
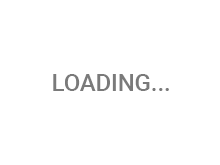
6. Cement batching station
The cement batching station is equipped with clinker, gypsum and auxiliary material warehouses. Weighing feeders are set at the bottom of each warehouse to give various materials quantitatively according to the set ratio. Clinker bulk facilities are also set at the side of clinker batching warehouse for external use of clinker. After the materials are discharged in proportion by the feeding metering equipment, they are sent to the ball mill by the belt conveyor for grinding.
7. Cement grinding
Cement grinding is not only a post process of cement manufacturing, but also a process with high power consumption. It is mainly used to grind the cement clinker (and gelling agent, performance regulating materials, etc.) to the appropriate particle size (expressed in fineness, specific surface area, etc.), the grinding materials are sent to the high-efficiency powder concentrator by the bucket elevator for sorting, the coarse powder is reground and continues to be ground, and the finished cement is collected by the air box pulse bag dust collector and then transported by the air chute The bucket elevator is sent to the finished cement warehouse for storage.
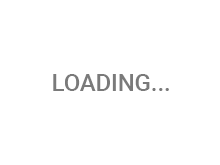
8. Cement packaging
After the outbound cement is unloaded by the unloading device at the bottom of the warehouse, it is sent to the cement packaging workshop and cement bulk warehouse by belt conveyor, bucket elevator and air conveying chute. The cement is packaged by an eight nozzle rotary packaging machine. The packaged bagged cement is sent to the finished bagged cement warehouse for storage through the bag unloading and conveying system, and can also be loaded and shipped directly. The cement bulk warehouse is equipped with cement truck bulk facilities for truck bulk.
Note: the material conditions provided by the end user shall prevail.
Specification
item | value |
Applicable Industries | Construction works , Energy & Mining |
After Warranty Service | Video technical support, Online support, Spare parts, Field maintenance and repair service |
Local Service Location | Egypt, Canada, Philippines, Pakistan, India, Russia |
Showroom Location | None |
Video outgoing-inspection | Provided |
Machinery Test Report | Provided |
Marketing Type | New Product 2020 |
Warranty of core components | 1 Year |
Core Components | Engine, Gearbox, Motor, Pressure vessel, Gear, Pump |
Condition | New |
Place of Origin | China |
| Zhejiang |
Brand Name | TongLi |
Voltage | 220/380/440v |
Power | 800-20000KW |
Dimension(L*W*H) | Depending on capacity |
Weight | 850000kg |
Certification | CE,TUV,ISO,BV |
Warranty | 1 Year |
| Online support, Free spare parts, Field installation, commissioning and training, Field maintenance and repair service, Video technical support |
Key Selling Points | Energy saving |
After-sales Service Provided | Engineers available to service machinery overseas |
Capacity | 100-6000tpd |
Color | Customizable |
Product name | Cement Production Plant Line |
Keyword | Cement Plant Cement Production Line |
Application | Cement Clinker |
Packing & Delivery
1.Standard container 2. Nude packing 3. Wooden box
Company Profile
Zhejiang Tongli Heavy Machinery Manufacturing Corporation is located in Tongxiang which is around sixty miles from Shanghai China. Set up in 1958 the factory covers more than one hundred and fifty thousand square meters. We possess one hundred sets of heavy machinery equipments, such as CNC horizontal lathers, CNC vertical lathes for turning, millings, borings, CNC Rollings, and cutting machines.
We specialize in heavy machinery equipment production, such as serious of ball mill, vertical mill and rotary kiln for cement in power, mining and construction industry, all kinds of granulator, dryer, cooler and coating machine for fertilizer industry. Our products have gained popularity all over China and exported to Central and Southeast Asia, North & South America, and Africa.
In addition, we offer parts of casting, machining and welding service for customers around the world. We are excellent at casting and machining design, such as working with Auto CAD, Pro-E, UG, and Solidworks, integration of customer new product development and prompt prototypes process which includes pattern making, casting, heat treatment, machining, assembling, and work testing etc. We could provide OEM/ODM according to the specifications, standards, and special requirements provided by our customers.
Quality is the life of our company. All of the products of Tongli have ISO 9001 Certification. Tongli provides you with great cost saving solution by offering your competitive pricing. Tongli is looking forward to welcoming customers abroad to visit our company and the opportunity to cooperate with you in the future.
FAQ
1. who are we?
We are based in Zhejiang, China, start from 2002,sell to Domestic Market(81.30%),Oceania(9.10%),Eastern Europe(4.60%),North America(3.60%),Southeast Asia(1.20%),Southern Europe(20.00%). There are total about 501-1000 people in our office.
2. how can we guarantee quality?
Always a pre-production sample before mass production;
Always final Inspection before shipment;
3.what can you buy from us?
Vertical Mill,Rotary Kiln,Ball Mill,Incinerator
4. why should you buy from us not from other suppliers?
Tongli Heavy Machinery Co.,ltd established in 1958year, is a member of the China Building Material Machinery Association, a
leading enterprise of China Cement Machinery, on the vendor of designated manufacturers for coal industry mechanical and
electrical equipments, ISO9001:2008 accredited and accredited as a high-tech & new technology enterprise of Zhejiang Province,
national designated “defend the contract heavy credit enterprise”, modern enterprise of national top ten cement grinding system of
technologies and equipment , at the top of cement equipment manufacturing in Zhejiang Province.
5. what services can we provide?
Accepted Delivery Terms: FOB,CFR,CIF;
Accepted Payment Currency:USD,EUR;
Accepted Payment Type: T/T,L/C;
Language Spoken:English,Chinese,Italian