payment terms: | letter of credit, wire transfer | application: | Industry, Vehicles, Power Tools, Motors |
Video external inspection: | if | Mold Type: | Tungsten steel |
Surface treatment: | High frequency quenching, oil immersion | Marketing Type: | normal product |
Spare Parts Type: | Powder metallurgy parts | Mechanical test report: | if |
Warranty: | 1 year | Macro Density: | 20 - 43 hours |
Micro-indentation density: | 60 HRC max | Showroom location: | not any |
Weight (kg): | 0.01kg | brand: | custom made |
type: | Powder metallurgy sintering | Health status: | new |
Material Standard: | MPIF 35,DIN 30910,JIS Z2550 | Applicable industries: | mechanical |
Material: | Iron/Stainless Steel/Bronze/OEM, Iron | product name: | Powder metallurgy parts |
Processing: | Powder metallurgy, CNC machining | place of origin; place of origin: | Zhejiang, China |
Supply capacity: | 300,000 pieces per month | port: | Ningbo/Shanghai |
After-sales service provided: | Free spare parts | Main selling point: | competitive price |
Packaging Details: | Packing: PE bag + carton + wooden box | Packaging Preview: | |
Local service location: | not any | | |
Product Description
commodity | Factory custom powder metallurgy products, processing metal powder metallurgy parts | | | |
raw materials | iron, stainless steel, copper, steel, iron, alloy steel | | | |
surface
| Induction quenching, oil immersion, rolling, electroplating, steam treatment, etc.. | | | |
| 1. High density of 6.7- 7.4 g/cm32. Hardness: HRC 30-50
3. Accuracy: ±0.01mm
4. No chipping, crack, burr, metal pitting and other defects
5. High productivity, high cost-effectiveness and energy saving
| | | |
Certification | ISO9001/TS16949 | | | |
Product display
illustrate:(1) Choose steel with strong compression resistance according to different strength and performance; (2) Use professional software and our professional engineers to design products with more reasonable size and better performance; (3) We can customize products according to customer needs According to the needs of our customers, the best performance of the gear can be exerted under different working conditions; (4) The quality assurance of each step ensures that the product quality is controllable.
main products
manufacturing process
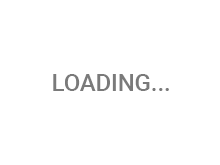
Advantages of powder metallurgy process
①High cost performance
The final product can be compacted by powder metallurgy method, which does not require or can shorten the processing time of the machine, which can greatly save materials and reduce production costs.
② complex shapes
Powder metallurgy allows obtaining complex shapes directly from the compaction tool without any machining operations such as teeth, splines, profiles, frontal geometries, etc.
③High precision
The achievable tolerance in the vertical direction of pressing is typically IT 8-9 (when sintered), which can be increased to IT 5-7 after sizing. Additional machining operations can improve accuracy.
④Self-lubricating
The interconnected pores of the material can be filled with oil, resulting in a self-lubricating bearing: the oil provides continuous lubrication between the bearing and the shaft, and the system does not require any additional external lubricant.
⑤Green technology
The manufacturing process of the sintered components is certified as ecological, as material waste is very low, the product is recyclable, and because the material does not melt, the energy efficiency is good.
Production equipment
Inspection Method
VIEW MORE