Voltage: | 380-3ph-50/60hz | Showroom location: | Canada, Mexico, Russia, Australia |
Weight (kg): | 2500 | strength: | 15kW |
Name: | Automatic engraving robotic arm | Packaging Details: | Standard wooden packing robotic arm cnc router for automatic engraving robotic arm |
brand: | Kuka | Work area: | 2000*2000mm |
Robotic arm: | Yaskawa | Mechanical test report: | if |
Core components: | engine | Supply capacity: | 5 automatic engraving robotic arms per month |
place of origin; place of origin: | China | guide: | PMI/HIWIN |
motor: | Yaskawa | feature: | 6 axes |
Video external inspection: | if | Core Components Warranty: | 1 year |
Marketing Type: | New Products 2020 | Packaging Preview: | |
Production capacity: | 10 sets/month | Drive System: | Yaskawa |
Dimensions (L*W*H): | 1500*1500*2000 15kw | Warranty: | 12 months |
payment terms: | L/C,D/A,T/T | application: | wood/foam mold, wood, stone, foam, mold, statue |
port: | Qingdao | Control System: | Yaskawa |
Applicable industries: | Hotels, Clothing Stores, Building Materials Stores, Manufacturing Plants, Machinery Repair Stores, Food and Beverage Plants, Farms, Restaurants, Home Use, Retail, Food Stores, Printing Stores, Construction Engineering, Energy and Mining, Food and Beverage Stores, Others, Advertising company | Health status: | used |
Spindle: | Italian Spindle | | |
4 5 6 axis cnc robotic arm engraving machine robotic arm for 3d engraving model cnc router price
Product Description
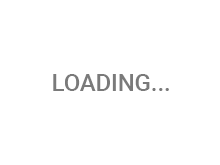
This system is suitable for the engraving of various batches of workpieces in industrial production, and is suitable for cutting, grinding, drilling and other processing of workpieces, as well as product modeling of wood, stone, aluminum alloy and composite materials. It cooperates with the parking machine, integrates the USP interface, and uses the offline programming system to process complex workpieces. The configuration can be changed at will, 100% perfectly compatible. It is very suitable for robot automation integration enterprises to carry out secondary development of products, with unlimited functions. The robot works well even in harsh environments, with a lifespan of up to 15 years and an average time between accidents of up to 70,000 hours.
KUKA KR210-R2700 robot is a new light-duty robot from KUKA. With a load capacity of 210 kg, it is especially suitable for engraving work. Whether mounted on the ground or suspended from the ceiling, the work can be done quickly and efficiently with extremely high continuous tracking accuracy and a working perimeter of up to 3100 mm. In addition, its modular design also makes it an economical solution.
technical parameter:
Load (referring to the load at point P at the front end of the 6th axis) | 210kg | |
extra load on the arm | 50kg | |
total load | 260kg | |
weight | 1068 kg | |
Movement axis | 6 | |
maximum envelope | 2696mm | |
Repeatability | <+/-0.06mm | |
Flange (6th axis) | DIN ISO 9409-1-A50 | |
controller | KRC4 | |
Installation location | on the ground | |
Motion parameters of each axis | range of activities | speed |
axis 1 | +/-185° | 123°/sec |
axis 2 | -5°/-140° | 115°/sec |
axis 3 | +155°/ -120° | 112°/sec |
axis 4 | +/-350° | 179°/sec |
axis 5 | +/-125° | 172°/sec |
axis 6 | +/-350° | 219/°/sec |
Milling System Integration
1: Pneumatic control unit3: Robot control cabinet
5: Cooling device
7: 7th axis guide rail (optional)
9: Electric milling spindle
2: Electrical control cabinet4: Linear tool magazine
6: Tool measurement and detection device
8: Robot body
10: Turntable (optional)
Machine Details
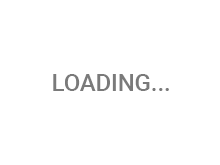
Italian Hiteco spindle
1. The motorized spindle can be lubricated with high-speed grease and oil mist according to different speeds.
2. The water cooling circulation system eliminates the temperature rise caused by the high-speed rotation of the electric spindle.
3. It has the advantages of high precision, high rigidity, high efficiency, large output power, low noise, etc., and the speed is fast
is 12000 rpm.
4. The universal HSK F63 standard tool holder is adopted, which can meet the customer's quasi-variable use of different processing tools.
Teaching pendant
Touch screen, graphic assistance, flexible interaction. The more powerful the robot, the more important it is to have an intuitive robot operator interface. The new KUKA smartPAD shows, on an ultra-high-definition, non-reflective touchscreen, how to control the robot intuitively with optimum effect. The intelligent interactive dialog window clearly shows the various processes to the user. At all times, users are provided with the operational elements they need at that time. Its purpose is to draw the user's attention to the most important factors, allowing it to work intuitively, simply, quickly and efficiently. Realize comprehensive intelligence.
Linear ATC System
The turntable is a single-axis positioner, which is mainly composed of a positioner frame, a servo drive motor, a precision reducer, a turntable, a lifting roller frame, a fixture and a control system. Among them, all welded structural parts are assembled from steel plates and profiles. All welds are welded according to the requirements of equal strength welds. Annealing treatment is carried out after welding to eliminate welding stress and effectively prevent deformation during processing. The engraving robot is composed of a 7-axis linkage automatic engraving system, which can greatly increase the engraving size of the workpiece and improve labor productivity.
Open KRC4 Control System
More efficient, safer, more flexible, and most importantly, smarter. The innovative concept of the KR C2/C4 provides a solid foundation for the automation of the future. Reduce automation integration, maintenance and maintenance costs. At the same time, the efficiency and flexibility of the system are permanently increased. Therefore, KUKA has developed a new system architecture with a clear
Structure and focus on using open and efficient data standards. All safety controls, robotic controls, motion controls, logic controls and process controls integrated in this system architecture share the same data base and infrastructure, which can be used and shared intelligently.
Workspace graphics
payload map
Application field
carbon fiber milling
Using a robotic system to perform the carbon fiber trimming process provides low noise and fewer maintenance cycles.
foam milling
Powerful programming capabilities so you can shape any material with a variety of tools, eliminating
it.
Robotic hot wire cutting
You can perform 2D and 3D modeling of any manageable material using a robotic milling cell, allowing hot wire cutting to provide a perfect and fast surface finish through polishing.
Marble processing
Marble cutting is optimized thanks to the use of a robotic system that provides a more versatile tool that allows for the highest quality cuts with less time and effort.
Robot on a straight track
Industrial robots on linear orbits offer increased precision, high speed, self-alignment capabilities, stiffness, and increased performance.
Orthopedic milling
Automation in the medical industry uses a wide variety of materials such as aluminum, titanium, stainless steel, etc... In this application, the speed and advanced technology offered by milling and turning systems are predominant.
polystyrene milling
Metal milling with industrial robots makes it possible to machine large, complex parts of small dimensions with high quality and precision.
Robot Art Milling
Through a simple interface, the robotic arm can shape any wooden surface to create the perfect architectural piece.
metal processing
Metal milling with industrial robots makes it possible to machine large, complex parts of small dimensions with high quality and precision.
Milling structure
Through a simple interface, the robotic arm can shape any wooden surface to create the perfect architectural piece.
Robot with turntable
This is one of the most effective tools when complementing a robotic system, it uses external
Provides greater safety and the highest quality axes when performing movements.
Yacht Robot Milling
Nautical machining is a challenging task, but the inclusion of industrial robotics has become a cost-effective manufacturing solution, as processes to be performed at large scale can be analyzed and designed through simulation programs.
Factory Tour
Luen Thai intelligent milling system is a highly modularized and integrated engraving robot workstation carefully built by Luen Thai. It is the most integrated and cost-effective engraving robot workstation so far. It adopts the high-end configuration of KUKA KR210 imported from Germany, a top robot manufacturer, and its complete set of operation control system. The engraving spindle adopts Italian Hiteco high-precision 10KW water-cooled electric spindle, and adopts standard HSK F63 standard tool holder. The tool detection unit adopts Marposs TS30 high-precision tool setter to ensure the accuracy of the tcp of the processing tool, thereby ensuring the processing quality. The workpiece rotating platform is specially designed and developed by our company for the robot engraving system, which can be linked with the robot. The software system is an international leading robot offline programming system introduced from AutoDesk. The robot system and the offline programming system are seamlessly connected and carefully built for only one purpose, making robot engraving and programming easier, product production more economical, and product processing adaptability better.
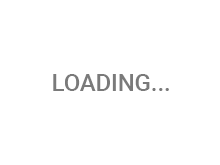
VIEW MORE